Tudor Watches: Sharing Secrets From Inside the Factory
In the luxury watch market, few brands are quite as secretive about their manufacturing and production operations as Tudor Watches. Being the sister brand to Rolex has its perks in terms of resources, R&D capital, and so on, but in trade much of the brand’s operations are kept behind closed doors — at least until very recently. To celebrate the inauguration of its brand new manufacture, Tudor recently invited select press from around the globe for a tour of the new facilities.
Arriving in the hills of Le Locle — the same watchmaking mecca home to the likes of Zenith and Ulysse Nardin — Tudor’s new space is both far from home, and right where it should be. Prior to this, Tudor occupied the space adjacent to the Rolex headquarters in Geneva, further cementing its position as living in its big brother’s shadow. In its new location, the brand is a stone’s throw from its supply chain, which in turn keeps its production and assembly processes much more seamless.
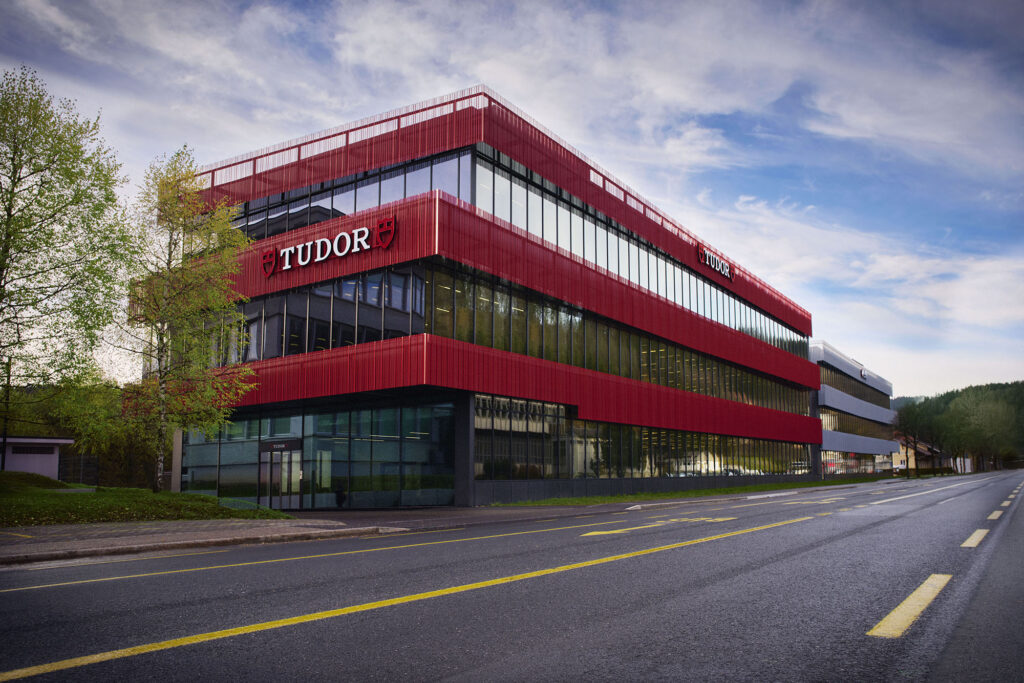
What’s especially interesting about Tudor as a business model is how the brand tackles a mix of what one might call diagonal integration. On one end of the spectrum, half of the building houses the Tudor-owned movement manufacturer known as Kenissi. The movement manufacturer is responsible for supplying all of the in-house mechanical watch movements that power Tudor’s watches, all while selling a small percentage to outside sources, including TAG Heuer and Bell & Ross.
When it comes to the balance of its watches — dials, hands, cases, and so on — Tudor relies on a network of suppliers. This method is the norm across the vast majority of the industry, however, Tudor being Tudor (and Rolex being Rolex), the brand has a slightly different approach. Every component supplier that Tudor uses is either fully owned or majority-owned by Rolex/Tudor. This ensures that the brand takes top priority when it comes to its supply chain, and that it has the ability to make requests and set requirements in a manner that simply wouldn’t be possible with an unowned third party.
Walking through the doors of Tudor and Kenissi for the first time, it was challenging to gauge what to expect. On one hand, once you’ve seen one watch manufacturing facility it’s a lot of the same, but the unique position of Tudor as a luxury value proposition with Rolex-level standards changes the equation quickly. Due to the supplier integration, there’s little in the way of true manufacturing taking place, for one. Big as the building is, the Tudor and Kenissi facilities are assembly plants more than anything.
Even in that respect, Tudor does things a bit differently than what’s seen at other brands. You’ll often see top-tier luxury watch brands where the assembly of a watch and its mechanical movement is completed by a single watchmaker. At the entry-level end, you’ll see more of an assembly line method, where each watchmaker is trained in a particular step of the process. At Tudor, it’s a bit of both.
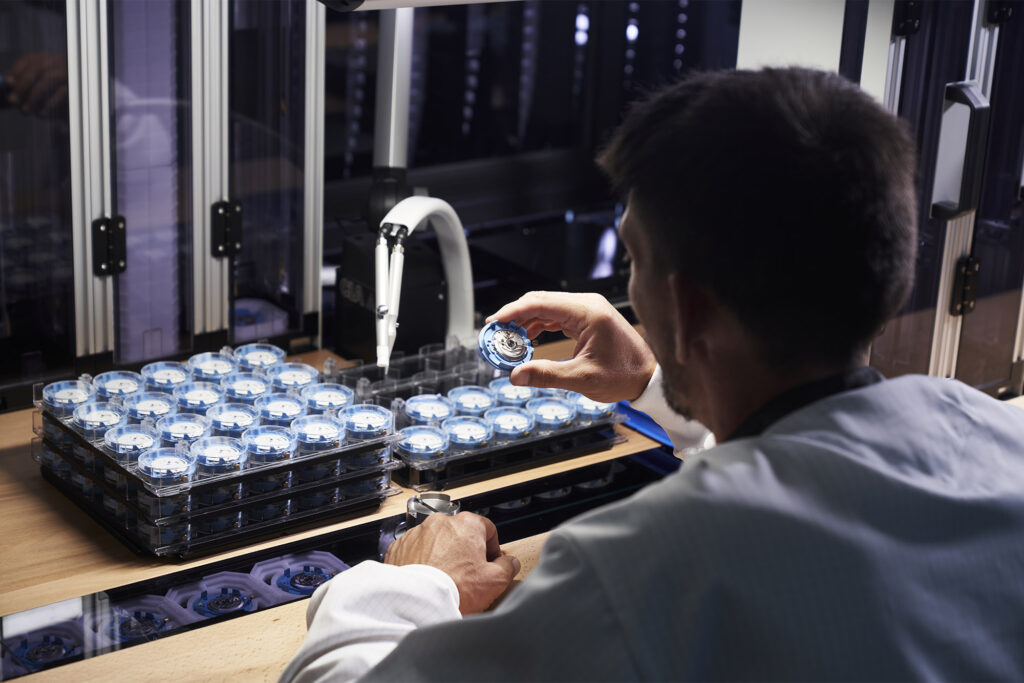
In Tudor’s main assembly area, there’s an array of workstations where its highly trained staff work on installing dials, hands, and completing other final assembly stages. Though each workstation is different, all of Tudor’s watchmaking staff have been trained in each step of the process and can complete the work on any of the brand’s roughly 700 catalogue references. Each team member is a specialist in all things Tudor, which ensures that no matter what happens there are team members in the room available to keep the production line moving.
Being a brand new facility, there’s little surprise when it comes to the level of automation in the room. From the brand’s secretive parts storage vault (the one room of the building where no photography is allowed) to the extensive testing and quality control department, a healthy assortment of robotics are deployed to keep processes smooth and standardized. Perhaps in part out of novelty, there are even a pair of roaming droids used to move trays of completed watches between testing stations.
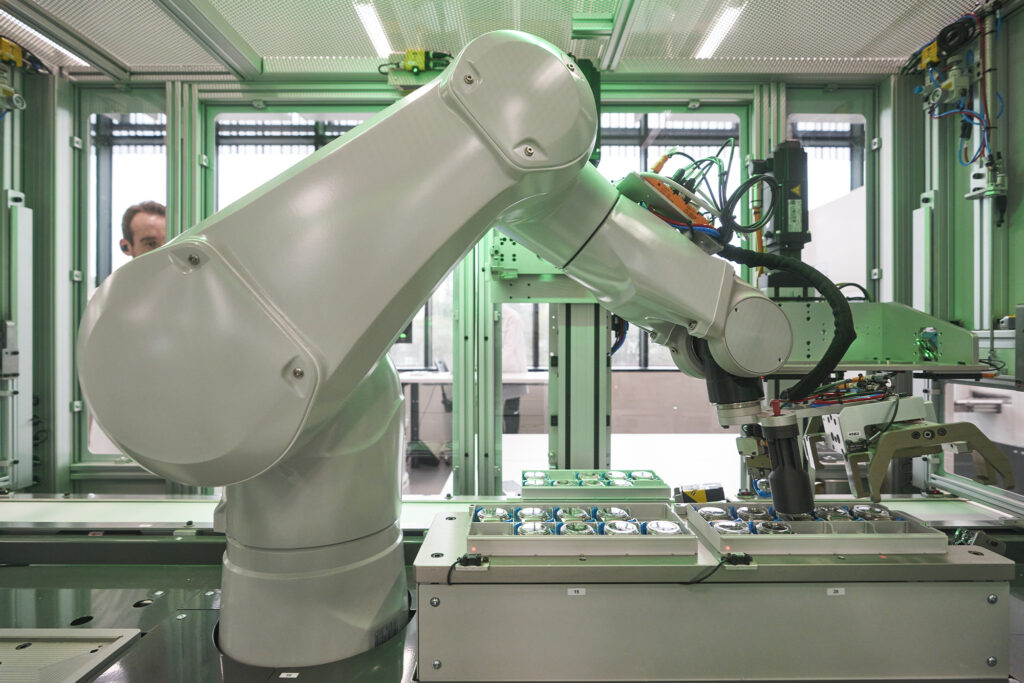
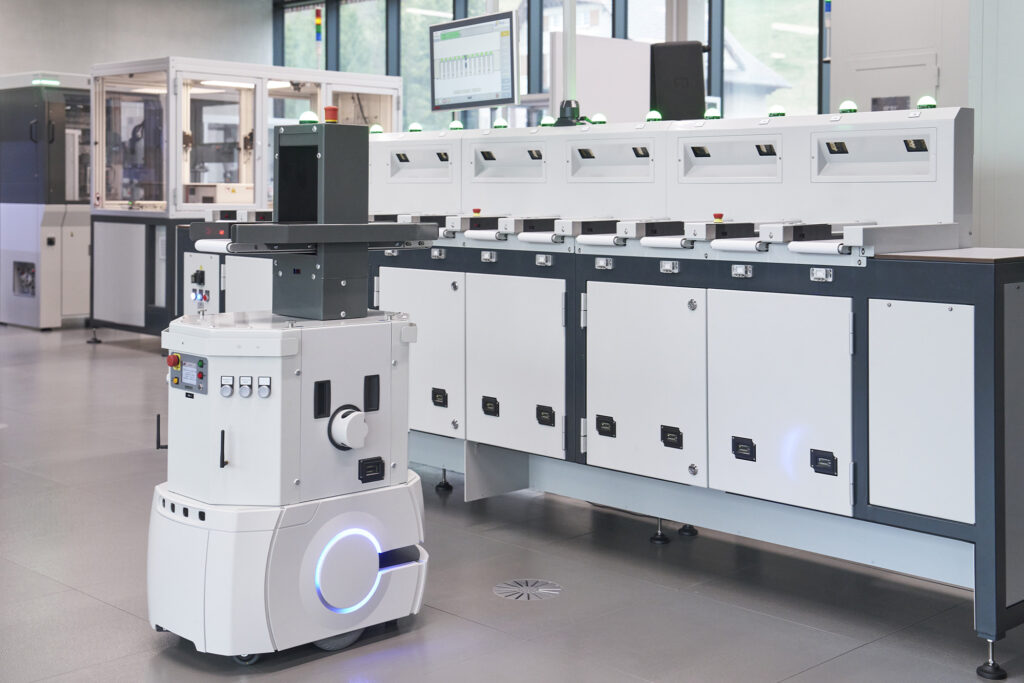
Given Tudor’s explosive popularity in watch collecting circles over the past decade, all of this focus on efficiency and keeping product moving is of little surprise. Just like big brother Rolex, annual production figures are kept quite hush-hush, but between the size of the location and the fact that it runs as a “zero stock” facility (with all watches heading straight from Le Locle to distribution and retail), it’s safe to say that business is good. With the quality of the product we’ve seen and the legacy of being “the Rolex for the people,” it’s easy to see why.